Hi friends! Apologies for the late update, I feel I’ve updated everybody everywhere apart from here – the one place I definitely have to. This issue has held up more progress than it should have, because of my funnily wired brain, but we’re back on track now. Also, I decided (well, my brain decided) I couldn’t progress with the next figures til this had been typed out.
What’s the delay? The first wave of minis are supposed to be in people’s hands already, right? WE HAD A SMALL HICCUP. Just a lil one. Kinda. I turned it into a teaching opportunity, of course!
Before I go into those details further, the shorter version is:
They will be coming very shortly, there were delays caused by changing a part of the sculpt of Julie D’Aubigny and finding a suitable company to print and cut the cards, which are both done, yay! HOPEFULLY, most will ship by the end of this month.
What happened?
It was entirely my own oversight! When designing a miniature, there is much more at play than what simply looks good. The miniature must be able to be cast many, many, times without fault; there is a fair bit of engineering that goes into making sure that works.
First, let’s look at the Version One. A stunning miniature, you will agree, and top paint job, John! This angle shows very well how one “one plane” this mini is. You could trace a straight line from the tip of her sword, up her arm, up her face, right up the bridge of her nose, middle of her forehead, and back down the other side.
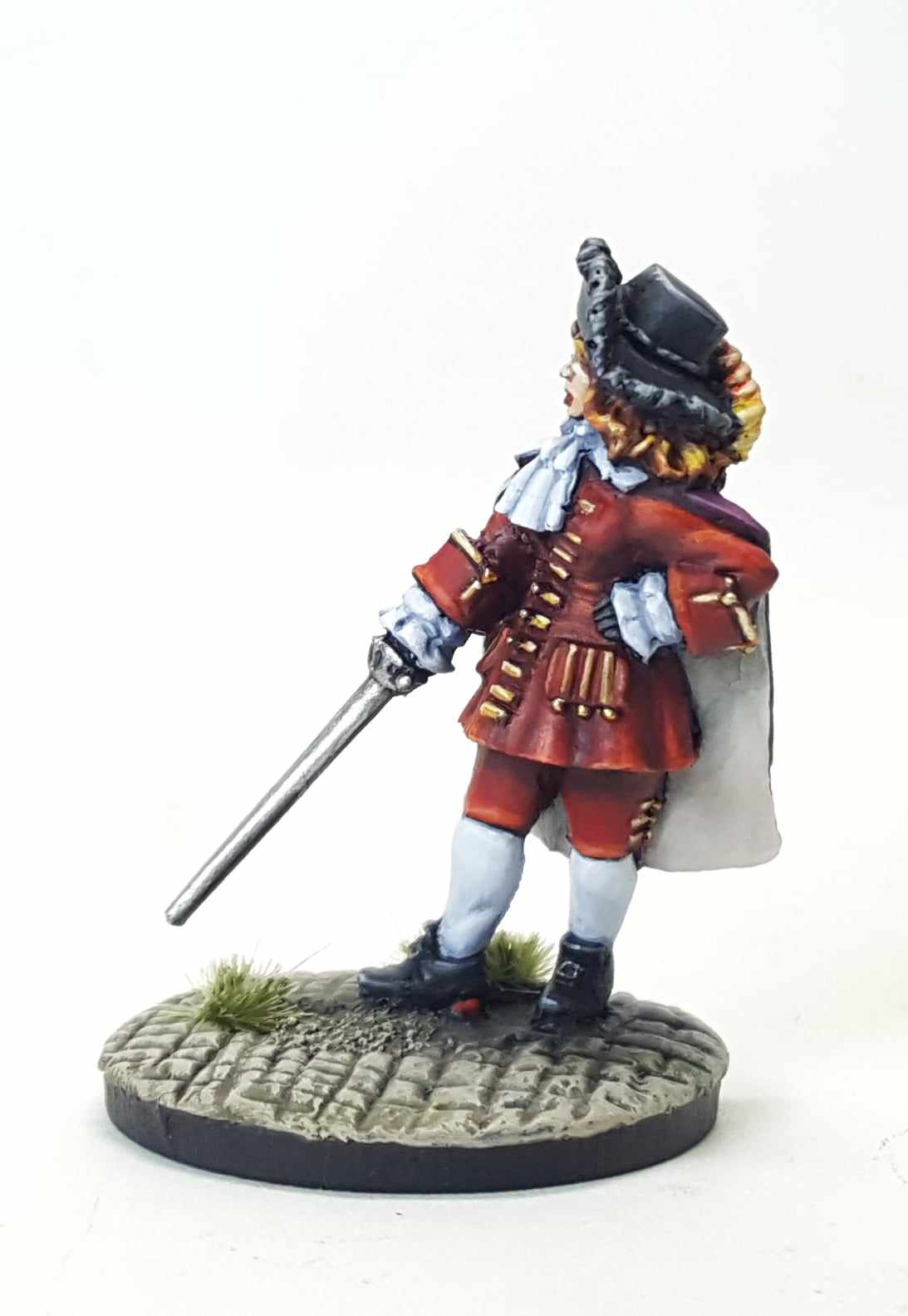

In terms of casting, this is a doddle. Figures get more difficult the more “planes” there are. Imagine she stuck her left hand out to point at us from the screen, that would complicate matters. Also, she would be alive.
The issue is… what even is this line? A metal mould is made of two parts of rubber or silicone in big round discs. When the mini is being moulded, the sculpt is squished between the two under the golden combo of heat and pressure to make the cavity, which we later fill with metal to create the cast.
The point at which these two discs push against each other in the moulding process is often called the “mould line”. These can vary from extreme to a mere feather, we like to pride ourselves on being the feather variety! Although sometimes they can be more prominent depending on the figure design.
The sum up of all the above is basically that the mould line was going down the middle of the face. But this project will hopefully teach you a bit about the background of how minis are made and the tribulations we may run into on the way!
While our mould lines are barely visible, nobody likes it down the middle of the face. It’s such an important part. I should have spotted this before she went to casting, but stuff happens!

Of course, I waited until she had been painted, and a huge chunk of her had been production cast already before I decided she had to change. Had this been earlier, we would still be on track – doh!
Was she good enough or not in her current state? I couldn’t decide. The line was minimal, but it was on the face, which is a mega pet peeve of mine in my own hobby adventures, and it wasn’t the usual done thing for Bad Squiddo. But I knew I was fighting against time, as this project is so far behind.
I felt absolutely sick when I approached the caster asking for the sculpt back, as I knew there was potentially a big extra cost of resculpting and money lost on the castings (we can get a bit back by throwing her clones into Mount Doom, though) as well as contacting Alan, the sculptor. It was none of their fault, but I was worried they wouldn’t be happy with my choice. BUT I AM A SILLY. I have worked with these people for years, and they’re lovely, DUH! They were ace, phew!
The best bit was that Julie was almost intact. When a sculpt has been moulded, they’re often broken and sometimes pretty much just crushed to dust! I didn’t want to convert a cast. I’d built it up in my head as this major thing. So I was ELATED to see her pretty much as she was before the moulding. Sculptor Alan Marsh is a dream and converted her easily before shipping her back to the casters.
So how did he fix her?

Decapitation! I believe he chopped the head off to turn it more forward-facing, but it looks like it’s been pretty much resculpted, I am sure the framework stayed the same though. So, the head was chopped off at the neck, rotated, and plopped back on. Then, the resculpting of the face and hair and anything else that was knocked off in the process, as well as a general MOT as she had “seen some things”. Alan noticed part of the hilt was missing, which I totally hadn’t spotted, so multiple eyes are good! That was sculpted back on, of course.
Now, if you trace that same line up the sword and arm, it now goes over her shoulder and up the side of her face, where the hair is. A cheeky little hair of a mouldline in her curly hair is fine; you can scuff it off with a blade, and it’s gone, much better than performing facial surgery.
HOORAY!
This has now been master cast, approved BY MEEE, and is now in the production stages. Poor John Morris has to paint her again, exactly the same as last time, please, John!
The Pretty Cards
The Pretty Cards will be ready once MK2 Julie is painted! Also, I need to finish designing them, I hope to update this blog very soon with those drafts. I was using Julie as a bit of an excuse as I could have been designing the rest, but it has been very busy around Bad Squiddo, and the time has just flown by.
New Printers
The other delay was figuring out how these cards would work. I want them A7 with rounded corners. But when you order from printing companies, they charge SO MUCH just for rounded corners, especially on low number runs (just 100 of each design), it was going to be a problem.
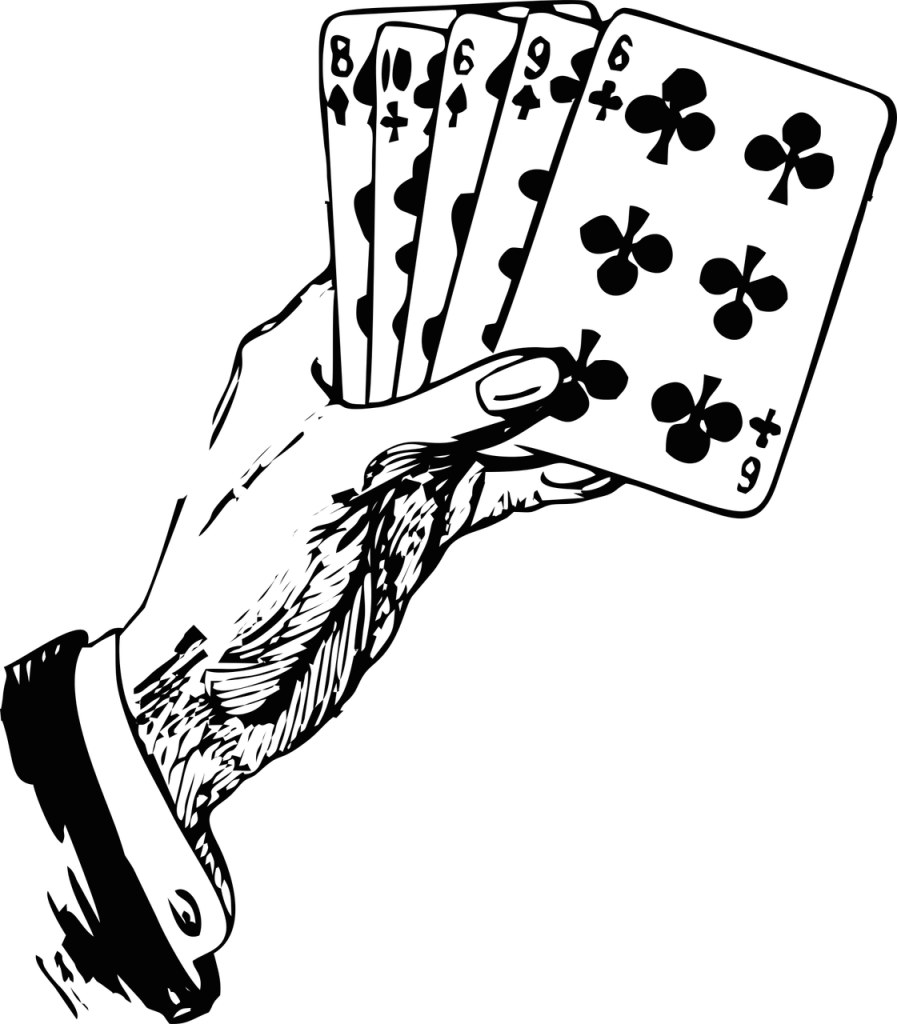
Investing in my own corner cutter even seemed an option – a heavy-duty one. I browsed through quite a few of those. They didn’t seem too great, though, really, the manual ones. Then it went into thousands of pounds, so I was back at the drawing board. That was until… I found a company! They seem really nice and helpful, and I met them in person and told them all about the project. I won’t name them yet in case it doesn’t work out (hehe, yes, I have made that mistake before), but it seems highly promising, and I’ll be going through some print designs with them next week. So, the delay was really useful in that sense, as I may well have found a new printing company for Bad Squiddo Games as a whole, not just this project. Yay!
Another accidental victory is that I really prefer the stance of the MK2 Julie, what do you think? I think she has more of a stronger “golden angle”. It shows how such a small change can create such a noticeable difference.
So there we go; silence doesn’t mean abandonment. I have just been pulled from project to project lately, and this week have a rotten cold (boo), but many wheels are turning.
Hooray!